Inventory Management: Sharing Best Practices
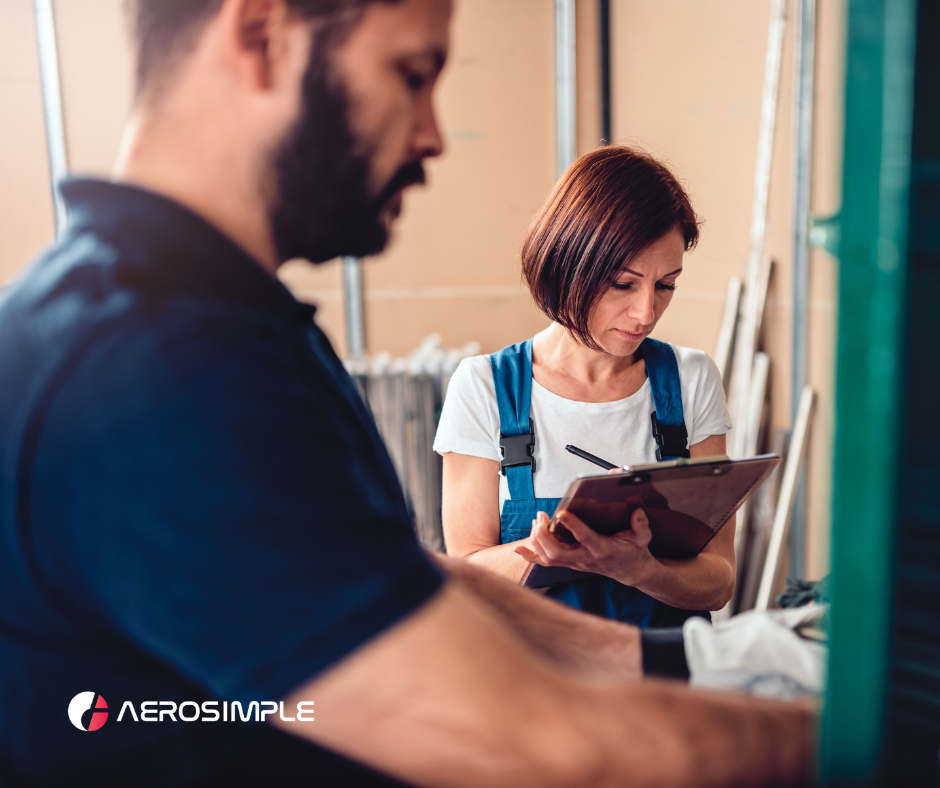
One of the most crucial—and occasionally least understood—factors in efficient airport operations is the provisioning of inventory assets. When inventory assets are properly provisioned, there is ample coverage when a maintenance event necessitates a replacement part. These maintenance incidents may happen either spontaneously or as part of a planned maintenance visit during normal operations (failure or damage). Despite the difference in their nature, each of these incidents is capable of disrupting airline operations. The inventory asset pool should be managed in a way that is both financially and operationally optimal. By maximizing the assets in the spare pool, a well-structured inventory plan will effectively achieve business dependability goals. Contact our Airport Operations Software professionals for more information.
Main Objective of Inventory Management
The paramount purpose of an inventory management system at an airport function with the single goal of making the right spare parts, at the right time available to the maintenance staff to avoid any cancellations and flight reschedules. It applies regardless of the operator's fleet size—whether it consists of a few planes or hundreds—and whether they operate on-demand charter flights, scheduled point-to-point flights, or a complicated web of domestic and international routes.
This article intends to give inventory managers a collection of ideas and procedures that will lead them to the best inventory-controlling solutions.
1. Sort the Inventory using ABC Analysis: Service parts are a substantial expense for businesses of all sizes, sometimes outpacing yearly benefits. The question remains here, do you handle all the items in the inventory with the same vigor? Or do some spare parts and materials require more focus than others? A traditional analytic technique that can help you with the answers is the ABC analysis, also known as the Pareto analysis. Understanding the criteria for categorizing the inventory is the key. Some of the common ways to categorize inventory are based on the frequency of use, dollar amount, and quantity. Here’s how ABC analysis works:
- A – List of spares and materials that are high-priority, high- value, high in demand, and require frequent reordering, and close stock monitoring.
- B – Items that are of medium priority, and mostly require bi-monthly or monthly ordering.
- C – These require the least control and pose minimum risk to the organization. These items are ordered once every 6 months or a year.
This method of sorting inventory promotes efficiency because it helps the inventory managers to carry the correct proposition of the stocks based on items classified as A, B, and C groups. They also get a fair idea of what items need the most focus and are crucial for the smooth functioning of the organization.
2. Create a central location for the inventory: Controlling an inventory that is dispersed throughout a facility is challenging. We understand that some of the spare parts are large and may require more space. But whenever possible store all the inventory at a single location together. It reduces the chances of theft, and loss significantly.
3. Restrict the access to the inventory area: This can be more challenging in smaller operations where technicians perform a dual role of working on an aircraft and extracting the items from the inventory at the same time. Whenever possible, let an inventory staff remove the items and hand them over to the concerned party. This stringent practice will ensure proper paperwork is in place, minimizing the events of misplacement of spares, or stocks falling below the threshold.
4. Regulate the receiving area: Recording information on the incoming parts is as important as the outgoing parts. Items should not be made available for maintenance until they have been entered into the inventory system, which should be under the supervision of inventory staff. Without proper tracking in place, spare parts may get installed without the knowledge of inventory personnel, which is not a good sign.
5. Have a technologically driven inventory management system in place: If you don't already have an inventory management system in place, then now is the time to unleash the benefit of automation to reduce your burden of tracking items. Automation makes it easy for airports to record all the details related to each part, like quantity available, its location, usage, and amount ordered. Using a cloud-based inventory management solution like Aerosimple, empowers the inventory manager to accurately gather and compile inventory data on a real-time basis. Additionally, automation also speeds up the process of recording transactions, standardizes some data types, and receiving triggers when the stocks fall below defined thresholds.
Understanding certain fundamental details about your inventory asset is a crucial management technique to allow you to stay in control of your organization’s inventory. Contact us today for a free trial of our inventory management solution.